LMFP-NMC battery technology with balanced energy density, safety, life and costs
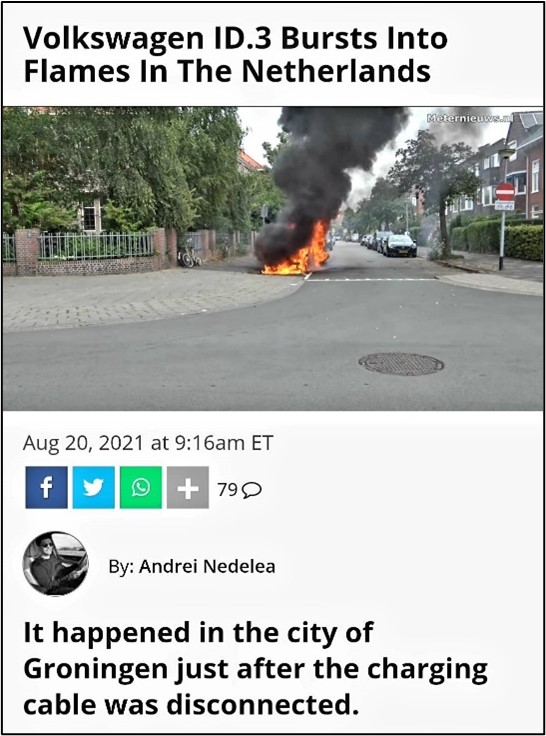
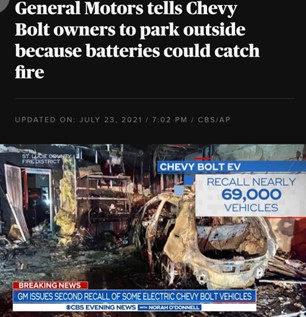
Figure 1 The NMC lithium battery electric vehicle fire accident occurred in Europe and America in recent years
Abstract
With increasing demand of high energy density batteries for electric vehicles (EVs), Ni-rich NMC batteries become the trend. However, safety and costs of Ni-rich NMC cells have been a great concern in the EV industry. In contrast, Lithium manganese iron phosphate (LMFP) with olivine structure has attracted much attention due to its high voltage (~4V), long cycle life, low cost and high safety. In this article, I will introduce the novel NMC/LMFP composite technologies (i.e. blended and dual-layered electrodes) that can provide the best solution to high energy density and safety, low cost and long-life Li-batteries for EVs and energy storage system (ESS).
Keywords:Lithium-ion battery, Lithium Manganese Iron Phosphate(LMFP), Lithium nickel manganese cobalt dioxide (NMC), LMFP and NMC composite、dual-layered electrode
1. Introduction
Since their introduction in 1990, lithium-ion batteries have made remarkable progress in performance. In the past 30 years, they have been widely used in products such as computers, communications and consumer electronics, and has had a great impact on human society. In recent years, in order to reduce human dependence on petrochemical and coal fuels, reduce pollution emissions, and alleviate global warming problems, various electric vehicles, solar and wind renewable energy have become the focus of development in the world. Due to the rich variety of positive and negative materials for lithium-ion batteries, lithium-ion batteries exhibit advantageous characteristics in different application scenarios. Today, the advanced small cylindrical "21700" battery has an energy density of 255 Wh/kg and 720 Wh/L and can support an electric vehicle with a range of 300 miles. And battery prices have dropped significantly from $1,000/kWh in 2006 to $120-140/kWh in 2021. lithium-ion batteries are already the technology of choice for battery electric vehicles (BEV) and energy storage systems (ESS). Nevertheless, researchers continue to improve lithium-ion batteries from three perspectives: (1) increasing energy density and lifetime, (2) reducing costs, and (3) increasing charging rates; these goals must be achieved without sacrificing battery manufacturability and safety. At present, Lithium nickel manganese cobalt dioxide (NMC) materials and batteries have high electric capacity, but their cycle life and safety are not good. Recently, NMC lithium battery fire accidents have occurred frequently (Figure 1), and various car manufacturers have also put forward higher requirements for safety.